by Josh Brown, global sales manager-laser plastic welding, Dukane
Until recently, laser plastic welding had a serious disadvantage: the inability to bond clear parts. While laser plastic welding has been aggressively adopted in a wide range of commercial applications for decades, adoption of this technology is driven by the obvious benefits over other joining methods like particulate-free joints, precision and incredible strength. Bonding clear parts posed a big problem for medical device and consumer products that not only need the precision advantages of laser welding but also often require fully clear assemblies. With new innovations in laser technology, applications from microfluidics and catheters to water bottles and earbuds are reaping the benefits of laser welding.
How 2μm lasers changed laser plastic welding
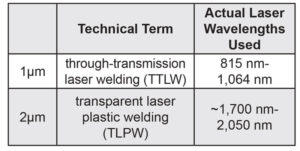
To understand how this new laser technology can help bond clear-to-clear applications, it is important to first understand how the original 1μm laser welding process works, and how it differs from the newer 2μm approach. Rather than utilizing a laser with wavelengths near the 1μm spectrum, as was the case in the past, this new technology makes use of higher wavelength lasers near the 2μm range.
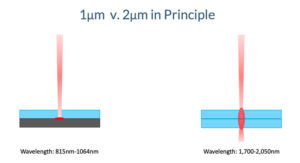
The originally developed process for laser plastic welding is known as through-transmission laser welding, often referred to as 1μm or “one micron” laser welding. In a 1μm welding process about 95% or more of the laser radiation introduced to an optically clear thermoplastic will transmit through the plastic. While less optically translucent plastics – such as PBT or plastics with glass fills – have a lower transmittance rate, they are still weldable if some of the laser energy can pass through the upper layer.
With the majority of the 1μm laser radiation transmitting or passing through the plastic, light energy cannot be transformed to thermal energy in the upper layer to create melt or a bond. Creating a bond with a 1μm laser requires the transmitted radiation to be absorbed at some point to create thermal energy. This absorption is achieved in the base component layer. The base component must have absorptive properties, which is easily achieved by adding carbon black to the resin or, alternatively, a special laser absorbing additive. The light radiation, once absorbed by the base layer, turns to heat and fuses both the upper (transmissive) and lower (absorbing) layers.
2μm laser welding primarily differs from 1μm welding based on how the higher wavelength laser interacts with clear or natural plastics without additives. The shift to a 2μm wavelength laser significantly changes the way a laser interacts with thermoplastics. With a 1μm laser, the majority of light energy is transmitted through clear plastics, whereas a 2μm laser still transmits some energy through the plastic, but a more significant amount of energy is naturally absorbed into the plastic – even if the plastic is optically clear. This is what makes all the difference.
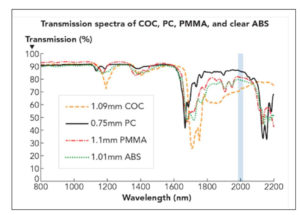
The graph (page 49) shows transmission rates for common, optically clear plastics at different wavelengths. The vertical blue bar covers the transmission rates at or near the 2μm wavelength. Notice the transmission is lower in this area than the transmission at or near the 1μm wavelengths. This is the “Goldilocks Zone” for 2μm welding where there is just enough absorption to allow for a strong bond at good production speeds.
For most naturally colored or clear thermoplastics, a 2μm laser will transmit about 70% to 85% of the laser energy and will absorb and retain the remaining 15% to 30% of the energy, without any additives. This absorption creates volumetric heating and melt throughout the joint interface.
Why choose 2µm?
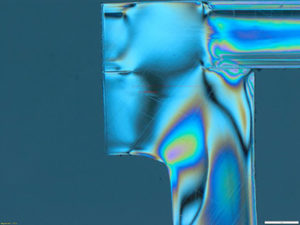
By now the primary advantage should be obvious. 2μm allows for the bonding of clear plastics without additives, but it’s worth understanding why this is important. Technically 1μm laser welding is capable of welding clear plastics, but it requires expensive and difficult-to-apply absorbers that increase costs and create concerns with biocompatibility and slight color changes. By switching to a 2μm process, companies can avoid additional material costs, maintain perfect clarity and decrease the number of steps and complexity in production lines.
Along with the ability to weld clear plastics without additives, 2μm laser welding comes with all the other highly desired advantages of standard through-transmission laser welding:
- Ultra-fine weld seams: beam spots of <0.3 mm can be achieved
- Repeatability: +/- 5 microns
- Various joint styles: excellent for lap joints, curved parts or radial joints (i.e., tubing, catheters, etc.)
- Sensitive applications: noncontact or light contact processing
Also, in recent years innovations in laser technology have allowed for significant increases in available wattages for 2μm lasers. Originally 2μm laser output was in the low double or even single digits watts. Now there are stable 200W sources available, resulting in drastically shorter cycle times and higher throughput.
Which applications are best suited to 2μm welding?
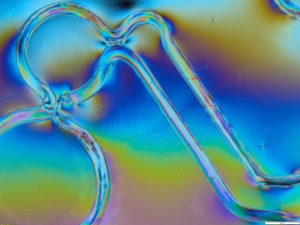
While 2μm lasers are being used in a broad range of industries – including automotive, general industrial, films and packaging – the majority of 2μm welding demand is coming from the medical industry. Typical applications include microfluidic devices, tubing, bags, connectors, catheters, on-body devices, diagnostic cassettes, fluid chambers and tanks, filtration devices and more.
Microfluidics, diagnostic cassettes and assays often require components to be transmissive in either the visible or UV spectra for analysis. Because of this, absorbers or colorants need to be avoided, often disqualifying 1μm welding.
Many microfluidic devices, such as the one at top left, utilize COC due to its low fluorescence, which can improve hyperspectral imaging and analysis.
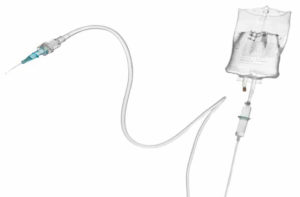
Other applications, including bags, tubing and connectors (at bottom left and page 52), often need to be clear so the end user can see the fluids inside or traveling through these devices.
The consumer products industry also is picking up on 2μm laser welding. Typical applications include water bottles, kitchenware, earbuds, cellphone microphone housings, battery housings, sensor enclosures, wearables, ink jet cartridges and hearing aids.
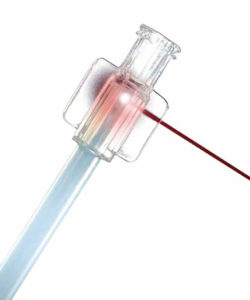
While the requirements for consumer products aren’t held to the same strict standards as medical devices, products are getting smaller, and aesthetic requirements are getting more stringent. Also, marketing teams often have as much, if not more, say in the selection of plastics and product colors as do the engineering teams – making it increasingly important that options are available for welding all colors and styles of plastics while retaining all of the clear advantages of laser plastic welding.
When is 2μm laser welding right for an application?
There are a number of factors that play into making this decision, but primarily – if the application requires all of the benefits that laser welding provides (clean joints, precision, repeatability, high-throughput) and for both joining components to be clear or optically transmissive – then it is on the right track for 2μm laser welding.
There are a few additional things to be aware of when exploring clear-clear laser welding.
Transmission v. optical clarity
It is important to note that laser transmission and optical clarity are not the same. When it comes to 2μm welding what is needed is transmission of IR radiation in the ~2,000 nm spectrum, not the visual spectrum. This means the parts do not necessarily have to be optically clear; however, this is typically the desired color format.
It is possible to bond colored plastics, even black plastics, if the materials do not contain absorbing compounds (i.e., carbon black). Typically, most inorganic dyes of all color types will allow for enough transmission to bond with 2μm laser welding.
Choosing the right plastics
Most natural thermoplastics will have some level of proper transmission-to-absorption and work with 2μm laser welding. However, some plastics are more difficult or impossible to weld. This is primarily a function of the transmission rate of the plastic at these wavelengths.
Recall that 2μm welding relies on a small percentage of the laser energy being volumetrically absorbed into the plastic, typically 15% to 30% energy absorption is ideal. What is needed is a “Goldilocks Zone” of just enough transmission to absorption to allow for a strong bond at good production speeds. If the transmission rate is too high, not enough energy will absorb to create a bond quick enough for most production processes. Alternatively, if the transmission rate is too low it can be difficult to weld through thicker components and get enough energy at the joint interface.
Most amorphous and/or optically clear plastics like ABS, COC, COP, PET, PP, PMMA, PS and PC work well with this process. Even PC, due to its high transmission rate at 2,000 nm, can cause issues – although these can typically be overcome with proper design of the part. Less optically clear plastics – such as PA, TPU/TPE and PE – can work as well but will have a lower transmittance, which can affect the thickness at which parts can be designed.
Semi-crystalline polymers also can be more difficult to weld due to the way the light energy scatters, making absorption more difficult. Some semi-crystalline materials, like PP, are weldable with 2μm, but materials such as PBT, PEEK and LCP are extremely difficult, if not impossible, to weld.
Part dimensions
Most laser welding applications rely on a galvanometric scanner to control the path of the laser beam. This allows for flexibility in weld patterns and part shapes. One major drawback of the 2μm process is the smaller working fields a scanner is capable of when outputting a laser in this wavelength. In order to achieve very small beam spots (<1 mm) working fields are typically limited to less than three to four inches. Larger working fields can be achieved, but beam spot size and accuracy are sacrificed, which is often not an option for larger microfluidic cassettes or applications.
To circumvent this issue, welding systems have been developed with a hybrid scanner plus servo driven XY stage. Using proprietary software, the scanner and XY stages can be synced to deliver the beam to the part with the flexibility of a galvo-scanner but also with the increased working field of a high-precision XY stage. In doing so, working fields of up to 490 mm2 (19.3 in2) can be achieved, allowing for large part sizes or the processing of multiple parts in a single cycle.
Is 1μm or 2μm welding better for more applications?
The laser plastic welding market has matured significantly over the past few decades and is still on a sharp growth trajectory thanks, in part, to innovations like 2μm welding and new color additives from material suppliers and compounders but not strictly because of them. So which process is better?
Truthfully, it just depends. While clear-clear requirements in medical devices and consumer products are leading a new charge for laser welding in these industries and opening new doors for applications previously out of reach for 1μm, the 1μm market still holds the lion’s share of applications.
Each application is different and has its own unique set of requirements, optical clarity being just one of them. The real benefit here is that the limitations for transmissive plastics in laser bonding applications are dwindling quickly.
What are the common steps to success?
While there is a growing amount of information available online about 2μm laser welding, the technology is still relatively new, and there are many applications that have yet to be explored. It is highly recommended that before settling on 2μm, potential customers should consult an expert who can help determine viability and a path to success. Typical steps should include:
- Discovery and data gathering
- Materials evaluation
- Design reviews
- Material sample or chip weld tests
- Prototype samples and proof of concept
- Equipment and production solution evaluation
The more information provided, and the earlier a welding expert is involved, the better. Answers to the following questions should be at least partially known to receive the best feedback and support:
- What materials or range of materials is to be welded?
- Are there color requirements?
- Will the materials have fillers or additives?
- Are CAD or drawings available for review?
- Is there flexibility in the part design?
- Why choose laser welding? Have other bonding methods been explored?
- What are the requirements of the weld and the assembled part in general (i.e. hermetic seal, bond strength, pressure or leak rating, light transmission, etc.)?
- What are the expected annual production quantities over time?
- Is there a cycle time target?
Established in 1922, Dukane is a diversified global manufacturer of advanced technology products. The company designs and manufactures plastic welding products for different manufacturing operations around the world. Among the many markets served by Dukane’s products are the automotive, medical, food and packaging industries. A privately held corporation for more than 95 years, Dukane’s principal manufacturing and distribution facility is located in the western Chicago suburb of St. Charles, Illinois. For more information, visit www.dukane.com.