by Paul Uglum, president, Uglum Consulting, LLC
Few activities have a greater impact on a business than the introduction, or expansion, of in-house decorating processes. Plastics decorating consists of a diverse and ever-expanding collection of fundamentally different secondary processes. New technologies and methods are continually being introduced. Improved UV cure systems, direct-to-part ink jet printing, new processes for part preparation and coating application are just a few examples of continuing developments leading to opportunities to add to or expand in-house decorating processes (see Figure 1).
As the opportunities arise to bring new processes in-house, the use of a structured process to evaluate and introduce them into plants is critical to reducing risk and creating a smooth transition to serial production. Many tools exist, but it is easy to overlook some critical steps if you do not work from a plan. This is true both for purchased turnkey decorating lines and processes developed in-house. In the case of a turnkey operation, you can outsource some of the steps to the supplier, but it is still important to verify they are done.
First steps
Once a technology or a better process that is new to your manufacturing facility has been identified, it is important to understand both its technical requirements and the cost of implementation. Spend the time needed to learn and understand the process. When possible, do benchmarking and visit facilities using the chosen process. Also, produce some proof-of-concept parts, either at the process supplier, in a development lab or at a supplier that is not a competitor. Making some demonstration parts gives the opportunity to better understand how the process works and provides samples for initial evaluation.
Develop a business case for the process early and update it regularly as more information becomes available. No matter how attractive the technology, if it does not make strategic and business sense, it should not be adopted.
Establish target requirements
It is important to know what constitutes success. Early in any project, it is critical to know what the requirements are. These can take the form of financial targets and expected first-time quality, as well as the expected performance requirements of the decorated part. Take the time to understand the requirements from the business side, the product performance side and the process side. Although useful, customer and industry specifications do not always capture all of the performance requirements needed for success. Look at current field results, look across industry specifications and be aware of changes in the target market.
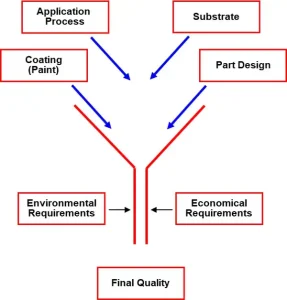
One of the more useful tools is the house of quality model. A simpler way of documenting the requirements and exceptions is to create a list, then prioritize and group the requirements. For each requirement, document the method used to measure if the acceptable performance. This will give you a working list of what is most important, what is required and can be shared with your suppliers, so they clearly understand what is needed and how to demonstrate success. This list captures both the target performance and the constraints that limit the available process window (see Figure 2).
Facilities specification
Each process has requirements to work correctly. Obviously, adequate utilities and some level of climate control for both temperature and humidity are expected. Requirements for different processes and materials are not always the same, so some level of isolation may be needed to meet the needs of each process. Also, processes that involve the evaporation of solvents or possible chemical exposure must be designed to prevent human exposure. All appropriate government and company regulations need to be documented early and designed into the process.
The requirement for an acceptable level of cleanliness in the surroundings often is underestimated. Even if the process is entirely contained, the issue can be contaminants carried into the process on the parts or operators. Cleanliness must be designed into the process.
Care should be taken to isolate lines from processes with different requirements or ones that produce contaminants that can be carried into the new production area. For example, aerosols from stamping or cutting processes can be devastating to decorating processes which require good adhesion. Shortcuts are bad. Putting a new line in the available space without understanding and isolating it, if needed, to meet the required operating environment, often leads to unpleasant problems.
Some issues are not easily controlled and may require modification of the process from location to location. Operating requirements for higher altitude/low humidity environments are different from low elevation/high humidity environments. Humidity can be controlled, but air pressure is more difficult to control. This may require material modifications to allow for the difference in evaporation rates of solvents. It primarily becomes an issue if operating identical lines in very different locations.
The human portion
One critical activity is developing and implementing training for personnel. This should include plans to train operators, maintenance crews, and design and manufacturing engineers. Although this seems like a basic step, the result must be robust enough to respond to the current issues of staffing short falls and turnover. Relying on operators to train their replacements is not very effective if the proper tools have not been implemented. Critical information and understanding can be lost with each generation of training. Establish clear and understandable training materials that include the reasons why behind instructions.
Manufacturing equipment
Equipment documentation should include a clear specification (statement of work) and cost and lead time estimates. Current economic conditions are leading to long lead times for machinery. Create a list of capable and recommended suppliers for purchasing.
It is important to document preventative maintenance schedules, troubleshooting methods and a complete spare parts list. Make sure to estimate the time required for set-up and changeovers. Finally, have a clear buy-off checklist and ensure that the equipment meets expectations prior to shipment to the manufacturing location.
When part-specific tooling is needed, the process is similar. Start with clear specifications, maintenance plans and storage requirements. Cost estimates should include spares and the expected tool life.
Materials
The choice of materials, process parameters and machine are strongly linked. All should be developed at the same time. Poor choices in any of these will lead to poor yields or a product that fails to meet expectations. Documenting the materials used in the decorating process should include all available material information. Documentation should include the materials safety data sheets (SDS), technical data sheets (which include process requirements) and expected life in storage. Storage and handling requirements should be documented and a plan developed to ensure the materials entering the process meets standards. It is important to review and understand interactions between materials, especially if using combinations of materials and processes. Clear documentation will allow future supplier selection and material changes with minimal risk.
Design and process
The design of a part and the choice of the decorating process are inseparably linked. A great part that is designed in such a way that it is difficult to decorate, and a poorly designed part that is easy to decorate, both lead to disaster. It is important that the whole design community, including the product engineers and the manufacturing engineers, work together to create the best match of design and process. This is especially true if the engineering staffs are not collocated. Tools like design for manufacturing and design standards, that take into account not only the target outcome but also the process used to make them, are critical to success. No combination of design and process are perfect, but the goal is to make the operating window as large as possible to accommodate a range of designs.
Design failure mode and effects analysis (DFMEA) and design review by failure modes (DRBFM) are useful and are widely used in many industries. DFMEA looks at part design and identifies potential failures. Current methods of detection and prevention are identified and the resulting risk is calculated. Potential improvements are determined and the resulting reduction is risk is evaluated. Key product characteristics (KPCs) should be identified on part prints and incorporated in the process control.
DRBFM can be useful if the process is similar to existing processes. This tool focuses on the changes from previous practice and reducing the risks resulting from those changes.
The decorating process
Correctly operating the equipment is critical to success. After an optimum set of operating parameters and materials have been identified and demonstrated, the process can at best only match that outcome and can often introduce variation that can degrade the final properties and yields.
Process failure mode and effects analysis (PFMEA) looks at the process and the failures or risks that result for process related issues. The DFMEA and PFMEA are closely related and a change in one should result in a review of the other to see what updates and changes to risk result. Like KPC, key control characteristics should be clearly identified on the part prints and incorporated into the process control documents.
Most decorative processes involve more than one step; for this reason, it is useful to map the process. Look at the inputs to each step and the expected outputs. Look at which inputs are controllable, which are critical and which are noise (uncontrolled variation). Also document any standard operating procedures and establish process parameter specification limits.
Mapping the process flow from the standpoint of parts and materials is widely used. Do not forget to map the people movement and the flow of waste materials. These can have an oversized impact on part quality and yields. People are often the source of particulate and fiber contamination, so proper clothing, behavior and unnecessary movement are important to capture.
One often neglected aspect of the process flow is the amount of time between steps. This is especially true when the cure of a material advances over time or when exposure to contamination during transfer or storage is possible. It is important to establish the maximum acceptable time between steps. This is one of the reasons that continuous lines, rather than batch processes, are favored or required by many manufacturers and customers.
Process specifications and work instructions need to be complete and reflected in the control plan. Documented required practices and workmanship standards (use visual standards when possible) are also important. Expected cycle times and yields should be documented. In addition, design standards (requirements/limits) need to be communicated back to the design community so that future designs consider the capability and limits of the manufacturing process.
Measurement systems
It is important to complete evaluations of all of the measurement tools and process controls. Tools like measurement system analysis (MSA) and measurement system evaluation (MSE) are very useful. It is critical to know how accurate and reliable your measurements are if you are going to make decisions based on them. Complete the capability studies and confirm defect rates in parts per million meet the expectations.
Closeout and transfer
This list of tools is probably not all inclusive; add or modify them as needed to give the best result for your company. The focus should be choosing, up front, which are needed, and understanding how to use them effectively. Tools exist to help make good decisions and improve the chances of a smooth introduction that delivers the target performance. Using them without understanding the tool or the process can be a waste of time.
Many customers require that manufactures use some or all of the listed tools. Remember, they exist for the benefit of the plastics decorator. Do not count on customer auditors to be experts either. They sometimes lack understanding of specific processes and are known to give incorrect advice on some process issues.
At some point, the new process primarily belongs to the manufacturing plant. Just after that transfer it is good to take a second look. Once the new technologies or processes are in serial production, it is important to do an on-site evaluation to ensure the process is stable and issues leading to workarounds have been resolved. No factory information system takes the place of walking the line and observing the process as it runs. This is a good time to capture any changes or additional learning and make sure all documents reflect any new learning.
Paul Uglum has 43 years of experience in various aspects of plastic materials, plastic decoration, joining and failure analysis. He owns Uglum Consulting, LLC, working in the areas of plastic decoration and optical bonding. For more information, send comments and questions to [email protected].