by Paul Uglum, president, Uglum Consulting, LLC
There is no universally accepted definition of smart coatings. As a result, it is hard to identify and understand the range of options. Also, it is difficult to measure the size and scope of the market applications. As a working definition, a smart coating is a type of functional coating which has one or more properties that can be changed significantly in a controlled fashion by external stimuli. These materials sometimes are called intelligent or responsive materials. Smart coatings can include self-arranging (stratifying) coatings and self-healing materials.
Some consider smart coatings and materials to be a new megatrend, while others consider them a novelty with little commercial applicability. The reality is some place in between the two extremes. To be a smart coating, the coating must provide added functionality beyond the core decorative and durability requirements. This functionality is activated by some external action or force. To be a useful smart coating, it needs to add value to the final surface by being a cost-competitive solution or by being a solution that cannot be achieved with any other available method.
Smart coatings have found use in many industries and applications beyond plastic, ranging from construction to cosmetics. One of the most dramatic recent demonstrations of a smart material, smart surface application is the BMW iX flow concept car. The car was introduced at the 2022 Consumer Electronics Show (CES) and demonstrates the ability to change the vehicle color using an innovative e-ink wrap (Figure 1).
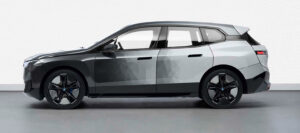
Smart coatings can be applied by any number of plastic decorating techniques, ranging from physical vapor deposition to conventional painting processes. Given the range of options, this article will focus primarily on conventional coating applications – such as painting.
Activating smart coatings
Since they are controlled by an external stimuli, there are several options for the activating source. It can be environmental (such as sunlight or heat in the environment), or the source can be applied on purpose to change in the way the coating or surface performs. If an external source is needed, it can be integrated into the surface that is being coated. This solution results in smart surfaces that go beyond just appearance and performance but can activate the desired outcome in a smart coating. These smart surfaces can include increased functionality and an integrated platform for lighting, switching, sensing and improved performance.
In order to work, smart coatings are designed to remain passive until demonstrating the desired function or change based on the stimuli. They must be able to repeat the process many times over the life of the product, which easily may be years.
Making smart choices
Smart coatings are one of a set of possible solutions to specific issues. The right answer for any specific application depends upon understanding all of the product needs. Repair or prevention of damage to high-gloss, piano black surfaces provides an example of an application where the various conventional and smart coating options are available. The right choice is the one that best meets the specific application’s needs, including cost and required field performance. In order to make the right decision, understand both the options available and the performance requirements of the application.
Classes of smart coating applications
The list of smart coatings seems never-ending: antimicrobial, anti-icing, self-cleaning, self-healing, color-shifting, self-stratifying thermochromic, piezoelectric and many others (Figure 2). A few that apply to plastics and composites are reviewed below.
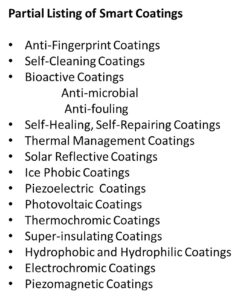
Antimicrobial
Antimicrobial coatings always have been an important target application due to the risk of healthcare-acquired infections (HAIs) and antibiotic-resistant bacterial exposure. The onset of COVID-19 significantly has increased the interest in, and desire for, self-sanitizing surfaces in applications beyond medical facilities and food processing. There have been significant advances in the past few years, and there is a greater acceptance of the cost associated with them.
Several barriers exist for their board application – the need for Environmental Protection Agency (EPA) approval of claims is one. The EPA, under the Pesticide Registration Improvement Act, has responsibility for setting criteria for measuring the efficacy of antimicrobial surfaces, such as painted surfaces. To that end, the agency has issued interim guidance with defined expectations. The time needed to achieve a 3-log reduction in viruses has to be less than two hours and the duration of the effectiveness has to be years.
Usefulness and public acceptance also will be influenced by the possible impact or cleaning of dirt impeding the performance of the smart surface. Any claims of antimicrobial performance will need to consider actual environmental life conditions.
Anti-fingerprint
Anti-fingerprint is a good example of an application that has increased need due to the use of capacitive switches in displays and as a replacement for buttons and knobs. In the case of displays, the optical distortion is the issue. With high-gloss finishes, the issue is unwanted and very visible fingerprints. A number of strategies exist. Once the fingerprint is transferred to the surface, it can be removed easily due to oleophobic and superhydrophobic functionality. In theory, transfer could be prevented if the functionality is extremely oleophobic and hydrophobic.
Another solution is using an oleophilic functionality that spreads out the offending print so that it becomes less visible. Finally, the transferred fingerprint can be broken down chemically over time due to additives and assisted by sunlight. Unfortunately, none of these provide an instantaneous solution and, in the case of relying on chemical breakdown, can be quite slow and take hours or days to return the surface to its original condition.
Self-cleaning and ice phobic coatings
Another new application is driven by the increase in vehicle sensing, as well as the need for clean lenses and covers for cameras, radar and eventually LiDAR used with autonomous vehicles. In-vehicle driver state sensing (DSS) systems require clean and undamaged surfaces to ensure optimum performance. Vehicle exterior surfaces often require some level of camouflage, as well as resistance to road damage. Finally, the buildup of dirt, water and ice can degrade performance. Other potential markets include the aerospace and renewable energy markets, like solar panels and windmills.
In many cases, the solutions are similar to anti-fingerprint coatings. Superhydrophobic coatings, unfortunately, do not always produce the expected result in preventing ice formation. Other options for ice phobic include freezing-point depression or oils to lower the surface tension of the coatings.
Self-healing
All surfaces, including coatings, are susceptible to scratching and abrasion damage from normal use. This not only affects appearance but can diminish other performance requirements, such as providing a barrier. Self-healing coatings are better suited to corrosion prevention; therefore, more applicable surfaces needing protection from corrosion or barrier protection. Several strategies exist to implement self-repairing coatings. One is the use of micro or nano capsules containing liquid polymerizable materials, which are released into the scratch when the surface is damaged.
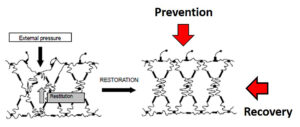
For plastic applications with high-gloss coatings, a more effective self-healing technology was developed by the Japanese paint company, Natoco. Its strategy is to combine a surface with high lubricity and a bulk functionality that allows the coating to deform rather than scratch and then recover over time (Figure 3). Additional work still is needed as the primary drivers for self-healing coatings for plastics remain durability and cost issues. The most common solution, when scratches in high gloss are an issue, is to use conventional highly cross-linked UV and combination UV / conventional cure coatings. Still, opportunities exist for smart solutions.
Passive thermal management
Solar and heat management coatings have a wide range of applications in both aircraft and construction industries. Forty percent of the energy from the sun is in the form of infrared and, in warmer climates, this can result in significant temperature increases. This creates an opportunity for smart materials in passive thermal management. Construction industry applications for roofs and windows are obvious, but thermal management also is important for any product used outdoors, including cars and aircraft. Additional applications include prolonging battery life in smartphones, shielding satellites and for protecting cars in extremely high- and low-temperature environments.
One recent development is the use of Vanadium dioxide (VO2), a phase change material in temperature-adaptive radiative coatings. Below 67° C it is transparent to infrared light; at temperatures above 67° C, it becomes reflective of infrared light. By adding Niobium, the range of the phase change can be tuned from 67° to -4° C.
Issues with implementation of smart coatings
Adoption of smart coatings depends upon the cost of the solution vs. the cost or performance benefit. Also, it depends upon the risk, loss of other desirable characteristics or the market desirability of the performance outcome.
As with any plastic decorating technology, smart coatings come with a set of constraints, while also providing advantages. The primary issues are the economics and the durability of these coatings. Automotive and aerospace remain the most difficult environments, as well as having cost and weight constraints. All products have requirements to ensure acceptable appearance and performance over their useful life.
In order to ensure successful implementation, the risk of new or unexpected failure modes should be evaluated. In addition to normal and accelerated validation testing, a design review by failure mode (DRBFM) should be conducted to document and reduce any potential failure modes.
Many smart coatings contain metal and metal oxide nanoparticles used to provide the smart functional properties. In other cases, they use exotic materials that are expensive and sometimes difficult to obtain. This drives cost up and creates issues with formulation and safe handling during coating production.
One significant issue with smart coatings applies to all new coatings. Coatings are complex mixtures that contain, in addition to the binder and pigments, additives and solvents to enable stability and processability. As the formulations become more complex, with the addition of responsive specific performance additives, the risk of failing to meet existing performance and durability requirements increases. When using nano-based technology, the manufacturing process also must consider both safe handling and prevention of agglomeration (even dispersion).
Learning more
Work is continuing on smart coatings, both at the academic level and in industrial R&D. Many references exist, ranging from industry magazines to scientific journal articles and books. It is worth taking the time to understand these advances through literature, conferences and discussions with major coatings manufacturers. The Smart Coatings ACS Symposium series, edited by Jamil Baghdachi, an Eastern Michigan University professor, is a good place to start reading. One of the best ways to learn more is to discuss the application with current suppliers of smart coatings and industry leaders.
Although not every development is commercially viable, each one may provide clues and the foundation to new solutions and applications. Take the time to understand the actual costs and value add before making any decisions. Smart coatings are only a smart choice if they meet the application’s needs and improve the product.
Paul Uglum has 43 years of experience in various aspects of plastic materials, plastic decoration, joining and failure analysis. He owns Uglum Consulting, LLC, working in the areas of plastic decoration and optical bonding. For more information, send comments and questions to [email protected].