By John Kaverman, president, Pad Print Pros
In pad printing, there are two distinctly different reasons for automating: low complexity plus high volume (processing the parts faster) and high complexity plus low volume (processing the print faster). This article discusses the benefits of both.
Part 1: Low complexity + high volume (processing parts faster)
Over the course of my career, I’ve often heard the term “automation” used in referring to both semi-automated and fully automated decorating systems or solutions.
In pad printing, semi-automated systems usually feature a human attendant (operator) manually loading and/or unloading some type of part-conveying accessory. These systems often are considered to be more flexible than fully automated systems in that they can be easily reconfigured to accommodate dozens of different part geometries simply by changing “tooling” (part nesting fixtures or “jigs,” cliché plates, transfer pads and cycle parameters). For example, a semi-automated pad printing system might be capable of printing a small appliance housing one day and an associated bezel the next.
Fully automated systems, by comparison, do not require a human attendant and are normally dedicated to a specific part or series of similar parts. Examples of fully automated systems might include dials for combination locks, wine closures and prescription eyeglass lenses.
In this article, the term “semi-automation” applies where human assistance is required, and the term “fully automated” applies where human assistance is not required.
Semi-automation
The benefits of semi-automating a pad printing system are easily quantifiable. By simply adding a rotary table to a single-color pad printing system, it is possible to realize a significant increase in throughput. Adding a rotary table enables the attendant to be loading and/or unloading parts while the printer is printing, increasing throughput by 50-60%, depending on whether the rotary table and printer are fully integrated.
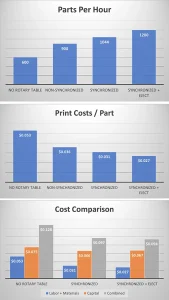
Fully integrated systems feature synchronized motion, meaning the pad printer and rotary table are moving at the same time, as opposed to the printer having to “wait” for the rotary dial to be in position before beginning the print cycle. Depending on the number of stations being utilized on the rotary dial, synchronous motion alone can yield an additional 16%+ over a non-synchronized dial. Further increases in throughput can be realized by adding a simple, single-axis part ejector. Chart 1 compares the various rates previously discussed.
Referencing the different production cadences in Chart 1, one can easily calculate the reduction in costs per part. Chart 2 compares costs to print 500K parts, one-color, with a single operator at $25 per hour, a 90 mm diameter ink cup with an adequate volume of two-component ink plus thinner, a 10 mm steel cliché, appropriately sized transfer pads (replacing every 50K cycles) at 85% efficiency plus disposal of unused ink at eight-hour intervals.
How do the costs of a synchronized rotary table and/or automatic eject affect the overall cost to produce? Chart 3 represents the combined costs to produce 500K parts with “buy-back” of the synchronized rotary table and the table with automatic eject.
As shown in Chart 3, combined costs are reduced by 24.22% with the addition of the rotary table, while the addition of the automatic eject decreases costs by an additional 3% for a total savings of 26.57% over the “stand-alone” printer.
Further cost savings can be realized when the end-user has the latitude to program the rotary table because more positions equate to more time on station (lower indexer time per cycle). For example, in applications where the system is not dedicated to one specific part geometry, a 12-station dial might be programmed instead to use six sets of two, four sets of three or three sets of four nesting fixtures for “families” of similar parts. This feature reduces the downtime required to change fixtures by allowing the operator to change fixtures with the touch of a button (no tools required).
Flex-feed systems
Flex-feed systems provide a viable solution for upgrading semi-automated pad printing systems to fully automated systems. Flex-feed systems feature cameras and specialized software that identifies specific parts from a batch of parts (by geometry or color, for example), communicating the location and orientation of those parts to a multi-axis robot that, in turn, picks the individual parts up, orients them and loads them into the pad printing system. For example, a flex feed system might be used to load randomly spaced and oriented combination lock dials on a conveyor, radially orienting and automatically loading them to a rotary table. When the color of the powder coating is changed on the dials upstream, a different (color-specific) file is loaded to the pad printing system to facilitate the accurate location and orientation of the new color. Alternatively, a flex-feed system might be used to load a series of parts having similar geometries (for example the “cluster” of cruise control buttons in the steering wheel of a car).
Fully automated systems
While fully automated systems may feature a flex feed system, they may instead feature dedicated, “part-specific” feeding, orientation and loading solutions.
Dental floss containers provide an example of a product that is commonly decorated in a flex-fed, fully automated system. Here, similar geometries might be transported on a conveyor with adjustable side rails to an interchangeable escapement, where they are then gravity fed or “pushed” into a rotary table-mounted fixture as it passes by underneath or loaded by a vision-guided robot as described in the previous scenario. A variable data code is applied to the side of the container as it moves from the load station to the pre-treatment station. After pre-treatment, the container is pad printing 1-2-3 colors in subsequent stations before it is dried (with hot air) or cured (with focused I.R. or UV) before being pass/fail vision inspected and, finally, automatically ejected to a conveyor that transports the printed containers to an adjacent blister packaging machine.
Deep-draw aluminum wine bottle closures (or “twist-offs”) are another example (see Image 1). Here, closures are dumped into a hopper having a capacity of several cubic meters, where they are elevated to a centrifugal-orientating bowl before being pneumatically fed (blown) down a track and onto the pad printing system’s rotary dial. Once on the dial, the closure might be embossed before being pad printed and/or foil stamped, pass/fail vision inspected and automatically ejected to an adjacent conveyorized drying tunnel, all with a rate of ~ 18,000 closures per hour single color or ~ 12,000 per hour two color.
Part 2: High complexity + low volume (processing parts faster)
While people have only considered high volume plus low complexity as a reason to automate the pad printing process, advancements in stepper- and servo-motor-driven pad printing technologies have significantly expanded the potential of pad printing systems to process the print faster in high complexity, low volume applications.
In distinguishing between the automated processing parts and prints, we are referring to complex decorating challenges where multiple images (or transfers) are required on multiple sides of a single part. For example, let’s look at some pad-printed ski boots.
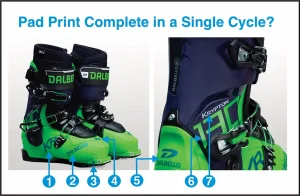
Looking at just the green portion of the boots (see Image 2), you can see five separate print locations on five distinctly different surfaces. Assuming that it is possible to pad print the “KR” and “DABLELLO” with two transfers in one setup, the green portion of the boot would require a minimum of four set-ups (side + side toe + top toe + heel = 4). Realistically, it would probably be five hits.
If the boots were printed partially assembled to include the black portion, it would have a total of seven transfers in five or six different print locations – all of which require the boot to be positioned at a different angle.
Using the latest in programmable, stepper- and/or servo-motor-driven technology, it is now possible to pad print objects such as ski boots in a single cycle. This technology eliminates the need for multiple jigs and setups while allowing for digital image placement accurate to 1/100th mm and 0.01° of rotation, as well as “linked programs” to allow for the printing of specific images multiple times (to build opacity of lighter colors on darker substrates), and the ability to “stack” programs. Stacking programs enables the end user to put multiple images on each cliché, and to utilize up to 12 pads and each pad up to four times (with automatic pad cleaning after each pass), for a total of 48 possible prints per cycle, in up to 10 colors.
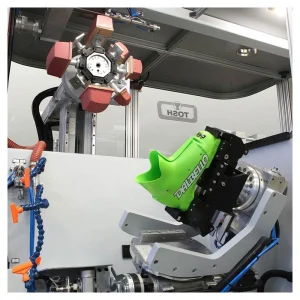
In addition to complex items such as the ski boots used in the example above, high complexity plus low volume systems have a variety of other uses. The systems are extremely popular in Europe for decorating toys, electronics, disposable medical devices and the heels of women’s shoes.
Pad printing functional materials
Decorating isn’t the only purpose for high complexity plus low volume systems: think “functional materials.” Functional materials include conductive and dielectric inks, radio-opaque inks, adhesives and lubricants. Potential applications include printing micro-circuits directly onto complex geometries, radio-opaque materials onto medical devices to allow surgeons to see exactly where their device is inside the human body, and adhesives and lubricants onto the surfaces that cannot efficiently be processed by other methods (such as spray or needle dispensing).
Avoiding the “vicious cycle of under-investment”
There is more to automating pad printing than simply bolting a robot to the floor next to a pad printer, especially if that pad printer is, technologically speaking, an antique. Look instead to integrate using a modern, 100% electric, digitally programmable stepper and servo-driven pad printing system. These systems are not “uni-tasking,” meaning that they can easily be reconfigured to accommodate varying ink cup and cliché dimensions, fully integrated, programmable part conveying accessories that provide fast, accurate part manipulation in multiple axes, and modular pad assemblies and cliché platforms that can provide multiple color changeovers of up to 10 colors in as little as 15 minutes.
Summary
Regardless of whether tasked with automating an application that is low complexity plus high volume, or high complexity plus low volume, make it a priority to develop a relationship with a supplier that has an engineering mindset.
Pad printing is an obscure process, and it isn’t widely taught as part of engineering curriculums anywhere in the world. If you have engineers that understand pad printing, you’re in the minority. Some pad printing suppliers do more work in certain industries than others.
For example, the companies that sell equipment for pad printing advertising specialties aren’t the same companies that excel at providing fully automated, high-speed automation with integrated loading, pre-treatment, vision inspection, drying/curing and unloading.
Choose wisely, because having a supplier with staff that can be considered an extension of the engineering department can be especially beneficial.
John Kaverman is president of Pad Print Pros, an independent consulting firm specializing in pad printing. Kaverman holds a degree in printing technology from Ferris State University, has over 35 years of experience in the plastics decorating industry, and lives in southeast Michigan. He can be reached at [email protected] and www.padprintpros.com.