By Paul Uglum, president, Uglum Consulting, LLC
Plastic decorating can be a treacherous endeavor. Although plastic parts are decorated using many different technologies, one thing is true for all of them, at some time or another there will be field problems. No matter how well run the manufacturing process, there always is a risk of field failure and unhappy customers. When this happens, one can become aware of the issue in several ways. It can be an urgent distress call from the customer over increased warranty or field returns. If vertically integrated and manufacturing the end product, it can be the final customer complaining or returning products.
So how should one approach the issue when it occurs? A lot depends upon the nature of the problem and the severity. In all cases, one should respond in several ways simultaneously. First, identify the problem (and its root cause), next ensure current production is to specification and adequate for the application, and lastly, protect the customer from continued exposure to unacceptable parts.
In all cases, it is critical to communicate with and protect the customer. This may mean verifying the current process is producing parts to specification, and if not, pausing manufacturing. If the issue is identifiable and measurable, there may be the need to sort out a stop gap solution. Decisions are not necessarily easy when in the early stages of a problem, the precise nature of the defect might not be clear and the root cause is unlikely to be clearly identified.
Initially, it is important to get as much information as possible about the defect and its cause. Start with a description of what the complaint is. Unfortunately, the nomenclature of decorating defects is not highly standardized. In some cases, defects that appear identical can have very different root causes. One may get a vague and not very useful description like defective paint. Describing a lump on the surface of a part as dirt, without establishing contamination as the root cause, can lead to wasted time when seeing corrective action. It is best to describe the appearance of the defect without speculation as to the cause. Pictures help, but it is best to obtain actual returned parts. Information usually comes in the sequence of verbal or written descriptions, then pictures and hopefully next, actual returned parts.
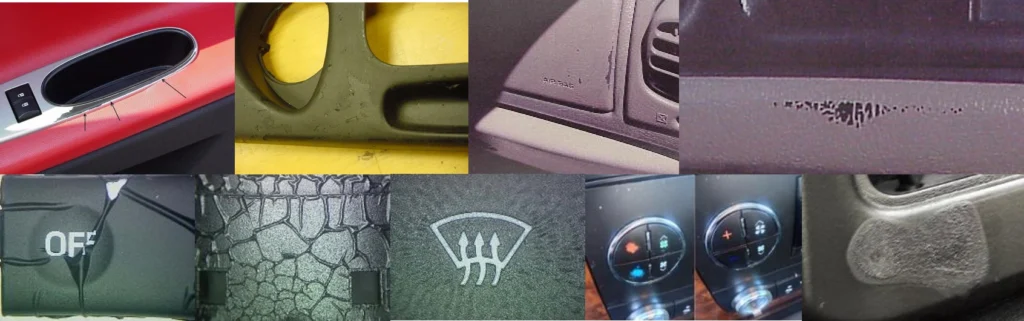
The information to collect includes: What is the defect (issue)? When was it found (and when the part was placed in the field)? Where was the issue detected (this can be very useful in establishing the use environment)? What is the impact (size and severity of the issue) and what is the frequency of the defect? One can never have too much information but should not expect all of the initial information to be accurate.
It also it important to determine if there really is a problem with the product or if it’s the manufacturing. The issue may be caused by the handling or shipping, poor specifications and inappropriate application or abuse in the field.
The cause of the issue can be materials, process or the use environment. In some cases, the raw materials, plastic, inks, coatings, etc., can be defective as received in the plant. In other cases, the manufacturing process may have varied from optimum conditions, to conditions that fail to fully cure or process the part. Finally, on the topic of field failures, in some cases, the use environment may have been improperly understood by the customer or may have changed over time.
It is impossible to predict what use environment changes may come in the future, but past examples include: the increased use of alcohol-based hand sanitizers due to the pandemic, increased use of insect repellants due to the Zika virus from mosquitoes and increased use of sunscreens due to concern about skin cancer. All of these were detected after causing field failures and the industry responded with more robust specifications, formulations and processes. Similarly, early soft feel coatings were susceptible to hydrolysis (in humid applications) and chain scission was corrected with more robust standards and improved materials.
Finally, in some cases there is damage due to customer abuse of the product. This can include improper and exuberant cleaning, as occurred during Covid, and actual physical damage due to impact with hard objects that not only damage the decoration but the underlying substrate. Remember physical damage also can occur in the plant or the customer’s plant, due to improper packaging, handling and assembly.
Important Questions
It is critical to define the nature of the problem and the scope of the problem. First notifications usually are verbal or written and are generated from field data reports (so at best are second hand). The best way to actually understand the problem and to analyze its cause is to receive actual physical parts from the field. Photographs and reports are not nearly as useful as actual parts and verbal descriptions are the least useful and can be misleading.
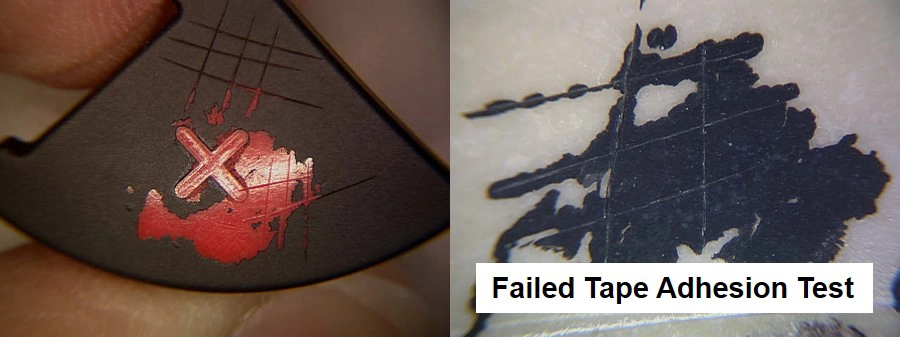
What is the failure mode? Is it coating softening, poor scratch resistance, bubbles in the surface, delamination of in-mold decoration (IMD), paint chipping, adhesion failures? This will lead to investigations as to the root cause. Determine if the damage is in one location on the part or if it randomly is located. Is it an observable manufactured defect, is it a defect that is invisible to test or is it a defect that develops upon use and field exposure? A part can appear good, but if the cure is inadequate, it significantly will be weaker in the field than a fully cured part.
It is important to know the time range when it was manufactured, when it was introduced to the field and time in the field. Was it defective as received, an infant mortality or did it occur after a defined time of use? When did the issue start? How long has it been since the defective parts were manufactured? Is it only found in some locations (regionally specific) or widely distributed?
The scope of the problem, how large it is in terms of the number of parts involved, over what manufacturing time span and after how long were the parts introduced to the field, defines the level of the risk to the business and, at the same time, provides clues as to the cause and solutions. Some issues are clear and simple, the part is the wrong color as received by the customer, others are complex and involve causes either in the manufacturing site or in the field (possibly a combination of causes).
Chemical Attack
Chemical attacks can be some of the most elusive to resolve. When the defect is a chemical attack, analysis tools such as Infrared Spectrometry, GC Mass Spectrometry and solvent extractions sometimes can provide clues as to the nature of the exposure. In some cases, damage is permanent such as softening of the coating leading to physical damage. In others, it is reversable. The coating is softened, but if it dries out, it returns to its previous state, and in some cases, the chemical penetrates the coating and damages the substate. This damage can be a chain scission (in polycarbonate one can usually find bisphenol A as an indicator) or it can be stress cracking the plastic (possibly indicating molded in stress in the part).
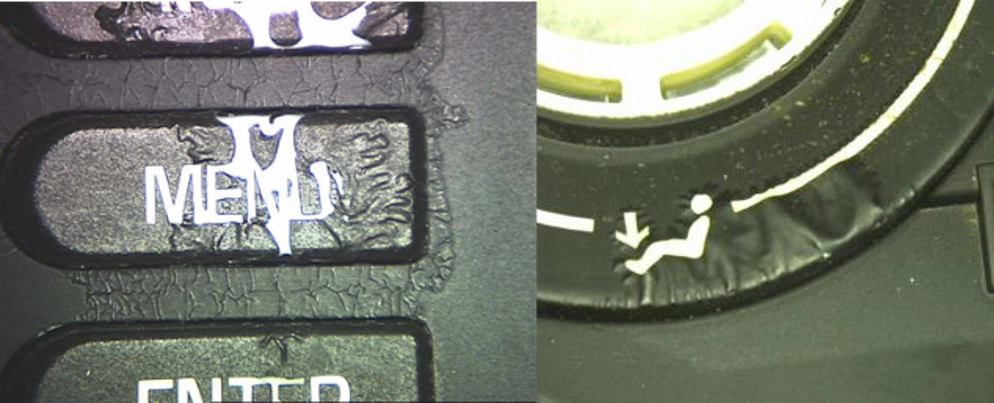
Structured Problem Solving
As one works the problem, it is very useful to have a defined process that documents information needed, who is working the issue, and next steps. Often a team with a clearly defined leader is needed to quickly respond to an issue. It always is important, when working a manufacturing problem, to have both someone knowledgeable in problem solving techniques and a subject matter expert in the processes and materials used. Ideally, these can be the same person but that often is not the case.
One should use a structured process for attacking the issue, there are many formats but in general they contain:
Description of the Problem
Structured problem solving begins with a clear definition of what the problem or issue is. This includes a description of the defect. This is where it is very important to look at actual failed parts and use analytical tools to confirm the visible failure type. Is it a production error, physical damage in the field a chemical attack or combination of causes? Be willing to revise the description of the problem as new information is discovered (comes in). Tools like Is/Is Not Diagrams, Timelines and Process Flow Diagrams are useful at this stage.
Identifying Potential Root Causes
In identifying potential root causes, actual data from a physical and chemical examination of returned parts is critical. After this, clearly identify potential causes. Remember, there may be two causes acting together to create the issue, chemical softening followed by physical damage, for example. Interfaces can be important, assembly processes such as gluing or optical bonding can lead to product failure. Tools like Failure Mode and Effects Analysis, Fault Trees, Cause and Effect Diagrams, Distinctions and Changes Lists, are all useful in this stage. Some of this may already be in place if the company has a robust Process Failure Mode and Effects Analysis, PFMEA.
Collect, Organize and Analyze Existing Data and Parts – Create New Data
The next step is to collect, organize and analyze existing data and data generated when confirming the process and materials are correct. In evaluating process and materials issues it is best to look at the data but trust how it looks. There is no substitute to going to the manufacturing line and walking the process from materials storage through part shipping. Observe the process and check to see that all process specifications are being followed and all manufacturing and test data are correct. Sometimes, what appears to be the smallest deviation, can be the cause of significant issues.
Check existing data including process control charts and manufacturing history (lots produced, and the materials used with each lot). Pareto Analysis of the returns and Capability Studies are useful at this point. If the defect appears during the production process the Shainin problem solving tools, like dictionary splits, are very useful in isolating the process step(s) where the cause is isolated.
Evaluate the Data Collected and Generated
Compare the identified possible causes to the facts. Can the failure be reproduced? Tools like the Contradictions Matrix Tool, catalog each potential cause and facts that support or contradict the problem’s root cause.
Collect Additional Data to Identify Root Causes as Needed
It always is best to have clean, newly generated data to ensure the reliability results. Techniques such as Response Surfaces, Statistical Comparisons, Characterization Experiments and Component Swapping are useful in further defining the root cause.
Determine Corrective Actions
Once the root cause has been identified, a corrective action plan needs to be developed. It should include actions to eliminate the root of the problem and implementation of changes to identify and eliminate repeat occurrences. Error proofing is an important part of this.
Validate, Implement and Standardize the Solution
If the root cause is materials or process, one of the critical tests is, if possible, to turn on and off the problem by replicating the materials’ deficiencies or process variation. An implementation plan and timing should be developed and shared with the customer. A capability study and implantation of the appropriate process controls are important with this type of root cause. A sampling plan and test protocol to determine if there are any recurrences should be established. It is useful to update all control documents and to prepare a look across chart to determine if similar issues occur elsewhere in the plant or at other manufacturing locations within the company.
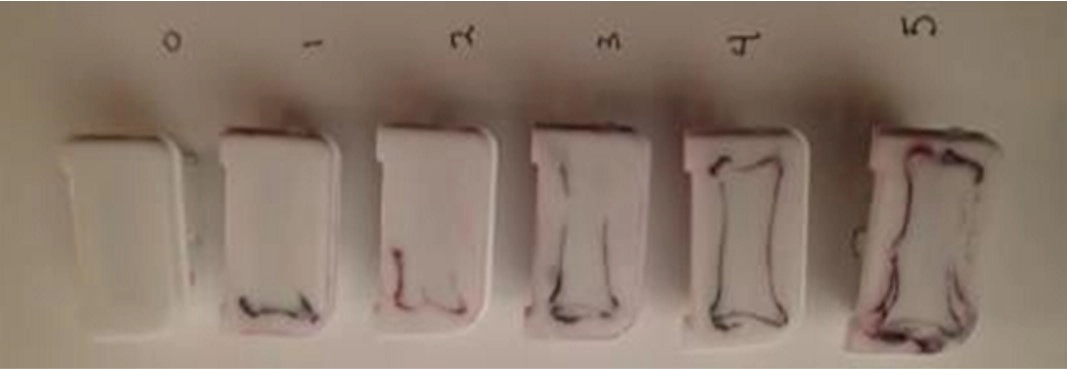
Final Comments
Do not just use one problem solving technique – use tools that provide the answers needed. Each problem somewhat is unique and the most effective tools will vary with each problem.
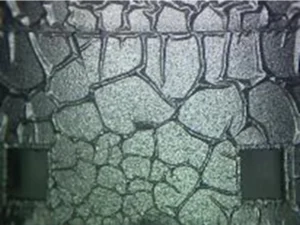
Finally, it is important to develop the skill set to quickly analyze and determine the root causes of manufacturing and field anomalies. Learn to use the tools before they are needed. Some like fault trees can be developed and modified as needed, to both improve the process and to systematically evaluate potential causes. Others like PFMEAs should be standard practice in all manufacturing operations.
Be vigilant and understand both how the product is performing in the field and how the use environment is impacted and changes over time. Too many specifications are rearward looking, protecting against past issues without protecting against future ones.