by Paul Uglum, president, Uglum Consulting, LLC
Metallic appearances have long been key to designs in the automotive field. They are an important part of the design portfolio and have been used for some time to create a high-end look. Just look at the vehicles with metallic grilles, door handles, accents, emblems and hubcaps. On the inside will be metallic door handles, knobs, badging, accents around the displays and controls, roof modules and many other applications.
Chrome features have been used in the automotive market since GM introduced them in 1926. Since first introduced, the number of technologies capable of achieving metallic appearances has increased and, with new innovations, continues to expand the available options.
Currently, the trend in the automotive industry is about luxury appearances and comfort. This push for improved aesthetics – as well as fit and finish – includes the use of textures, soft feel surfaces and, of course, metallic finishes.
What has changed in the automotive industry over the past few years are the options available, and the expectations of the marketplace that wants the latest styling, durability and green options. Some of these expectations conflict with each other. The best way to meet them is to understand the design capabilities and process limits of each of the options available.
What is new and what is established best practice
Options to achieve metallic appearances are many. The four primary technologies used to achieve these outcomes are electroplated plastic, physical vapor deposition on plastic, in-mold decoration of various types and thermal transfers.
Other alternatives that meet some of the appearance and functional requirements of metallic appearances include molded plastic with metallic pigments, painted plastic, in-mold or metal wrapped plastic and real metal features. The continuing success of thermal transfers used in both interior and exterior applications and the introduction of textured electroplated parts are two of the most promising growing technologies.
Plated plastic
The gold standard for metallic surfaces is still plated plastic, although physical vapor deposition and other alternatives are increasingly taking a market share. Plated plastic offers a wide range of appearances, cold-to-the-touch feel and can be used with clear coatings to further modify the appearance to provide a wide range of desirable appearances. Parts can be masked and two-shot processes used to produce additional appearances and create backlit features. The primary difficulty has been the waste stream and design limits of the plating process itself.
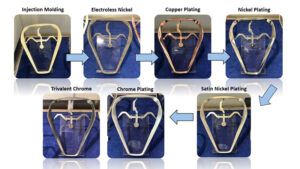
Chrome-plated plastic, also known as the galvanic process, consists of first molding a plateable plastic and then moving it through a number of wet chemistry processes. The first step is to etch the surface and apply an electroless metal. This is followed by several baths to apply copper, nickel and chrome in various thicknesses. These processes can produce a significant waste stream. Also, care must be taken in choosing the proper plastic – plateable grades of ABS are still the most common – and controlling the molding process to achieve the best surface for plating (Figure 1).
Traditionally hexavalent chromium electroplating was the primary method used worldwide. The future direction is to trivalent chrome, which has been adopted in Europe and Asia. Currently the dark chrome appearances favor trivalent chrome in the US but expect the transition to trivalent of all applications.
The change is driven by both the European REACH (Registration, Evaluation, Authorization and Restriction of Chemicals) regulation and by Environmental Protection Agency regulations, as well as by the increased costs of waste management. With the push to more sustainable processes the next step to improve the electroplating waste stream will be a move to chemical etchants that replace the chromic acid and perfluoro octane sulfonate (PFOS) currently used. The best way to learn about the plating options available and approvals is to go directly to the major plating chemical suppliers.
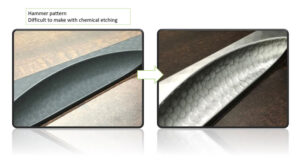
One of the newest innovations has increased the capability to extend the design portfolio by providing textured plated surfaces not previously possible in metallic appearances applied to plastic. These textured surfaces significantly increase the consumer appeal of plated parts. A tooling process of electroformed and laser-etched tools can be implemented to provide an easy-to-replicate textured surface that then can be plated.
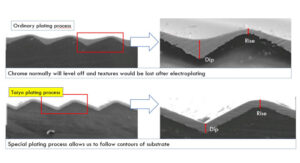
The advantage of this process over chemical etching is that it creates textures not possible with chemical etching, and the results between cavities in a tool can be identical (Figure 2). To take full advantage of this option, a proprietary process has been developed to control the uniformity of the plating coating to better replicate the plastic texture in the finished part (Figure 3). Textured, plated parts will make their first appearance this year in high-end sports cars. As designers see the extended range of appearances, expect more applications across the industry.
PVD
Physical vapor deposition (PVD) of metals onto plastic provides a wide range of capabilities. The process can involve evaporation of metals like aluminum or sputtering of metals and alloys to achieve a range of appearances and performance capabilities. Current best practice is to apply the PVD to plastic or painted plastic and then apply a clear or tinted UV cured overcoat to provide the needed durability.
The advantage of PVD as a solution is that it is REACH compliant and environmentally friendly. There are a broad range of color shades and effects, such as matte finishes, possible through the use of clear coatings. PVD also has good adhesion with a wide range of plastics. Since PVD chrome is thin, it is safer for impact in air bag emblem applications and is lighter weight than plated plastic. Since PVD can be applied thinly and still have a good reflected appearance, it also is easy to backlight for ambient lighting applications. PVD can be combined with other processes, such as painting and laser etching, to produce backlit graphics, selective lighting and other appearances. The primary limits on PVD have been the need for a coating to protect the thin metal and the costs of equipment necessary to produce parts. Although not yet used in automotive interiors, development of PVD coatings that can be used without a clear coating continues.
Thermal transfers
One of the most cost-efficient alternatives to electroplating and PVD is thermal transfer. Thermal transfers have most of the advantages of PVD, as well as a number of additional advantages. They have been in use at premium OEMs for over a decade and, since their introduction, the use has expanded into all levels of vehicles in all regions of production. The process allows for an environmentally friendly product that has high corrosion, weather and abrasion resistance both in vehicle interiors and exteriors.
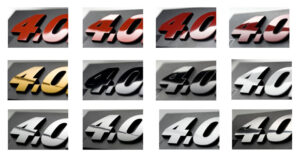
A wide range of unicolor metallic, bright chrome, as well as satin and tinted appearances is available and custom appearances can be developed (Figure 4). Thermal transfers can be applied both to as-molded plastic and painted surfaces, increasing the range of possible applications.
The cost efficiency is driven by two factors. First, two-part appearance can be achieved without having to use two-shot process or extensive masking. Second, because it is capital efficient, it is easier for tier one and two suppliers to bring the process in-house.
As the trend continues toward adopting more environmentally friendly and cost-effective options, thermal transfers are well placed to provide additional design options in both vehicle interiors and exteriors.
In-mold decoration
In-mold decoration consists of an in-mold ink transfer to the plastic surface. This can be designed to include a subsequent UV cured hard coat to increase durability. In-mold labeling consists of insert molding either a pre-decorated plastic film or a decorated applique.
The metallic appearance can be achieved either through application of metal by PVD or by very reflective inks. For automotive applications, the in-mold labeling process offers a wider range of applications and capabilities. In addition to providing either a whole surface metallic or selective metallic appearance, it can be used with backlighting to create ambient lighting appearances.
Finally, in-mold processes allow the production of parts that integrate several features, such as display windows and capacitive switches.
Critical factors
Decisions as to which process to use are often driven by the end use customer. The key is making the right material choice with the right design to meet the customer’s design intent, durability requirements and cost targets.
No one solution is ideal for all applications. Early involvement of the customer and suppliers will allow the best choice to be made. Failure to do this will significantly increase execution costs and problems.
Factors reviewed should be the intended part geometry, target appearance, performance requirements (make sure the customer-defined specifications are understood) and cost targets. Very high expectations exist for metallic surfaces. This is because they are highly visible, and it is easy to spot the smallest defect on reflective surfaces.
Also, remember that the best way to achieve a harmonious appearance is to make all similar parts using the same technology. This is not always possible, however, so if mixed technologies are used, it is better to have contrasting appearances than trying to make parts created with dissimilar processes appear the same.
Regardless of which technologies are chosen, do the research. There are many suppliers that can advise on the design limits and help with the design and technology tradeoffs. Work with both the customer and with the material, process and part suppliers.
A yet-to-be-determined impact will be what the current pandemic will do to global supply chains. Together with the supply chain interruptions, new regulations will, in all likelihood, change both the mix and the availability of various options.
Paul Uglum has 43 years’ experience in various aspects of plastic materials, plastic decoration, joining and failure analysis. He owns Uglum Consulting, LLC, working in the areas of plastic decoration and optical bonding. For more information, send comments and questions to [email protected].