Plastics Decorating
Like most decoration processes, there is a lot to consider when it comes to painting and/or coating a plastic part. Manufacturers and decorators should have a solid understanding of how that paint or coating will affect the final product. To that end, Plastics Decorating recently sat down with Akriti Agarwal, global project manager – paint and coatings, with Mercury Marine. Headquartered in Fond du Lac, Wisconsin, Mercury Marine specializes in outboard engines, the plastic components of which must stand up to some extreme situations. As such, the company and Agarwal know just how important it is to make sure any decorative element will hold up under pressure.
What should be asked of suppliers when sourcing for a new paint/coating for a plastics part application?
When we want to find a new paint or coating, especially for plastics, one of the first questions we ask is, “Can you paint Class A surface finish?” For plastic components, this is very important as Class A typically offers the most consistent color and gloss with fewer surface defects. For us at Mercury, plastics parts have to do more than just hold up to UV performance – they need to look the best they can. Not everyone can do Class A finish, so make sure to check your surface finish requirements with any potential supplier.
The second thing to consider and ask about is paint chemistries. Some shops work with acrylics really well and others are more experienced working with urethanes. Not every shop will be well versed in both. In that case, it comes down to the particular part and what paint chemistry is needed to achieve the desired look and performance? Oftentimes at Mercury, we want both the performance and the Class A system. Then we also want impact resistance, chip resistance and adhesion down to the substrate to make sure we get our customers a long-lasting surface finish. Talk to the potential supplier, ask what they recommend and what they can reasonably do.
Furthermore, it is important to make sure any supplier you work with is ISO-certified for quality control purposes. It also can be helpful to consider where they are located, although this is not strictly necessary. For instance, we are located in the Midwest, so if we can find a supplier who also is in the Midwest that can be very helpful in avoiding some supply chain issues.
What tests should customers perform to make sure the paint/coating selected is the best choice?
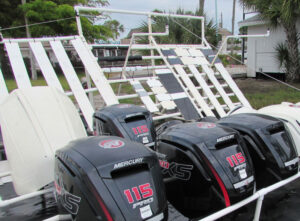
There are many tests that customers can and should perform, depending on the plastic part/application. For instance, at Mercury, some of the key testings we perform to validate a new supplier are color, gloss, orange peel, thickness, methyl ethyl ketone (MEK) solvent rub, cross hatch adhesions and pencil hardness. It is important to be sure testing is done not just for the corrosion or performance aspects but for the aesthetics as well.
For the stringent environments our outboards are exposed to, any new paint/coating system undergoes high-speed boat endurance testing to ensure these coatings can live and thrive in water just like our engines do. For this test, we paint complete outboards with the new paints and run them at high speeds side-by-side to current product. It’s a type of comparative testing to see how new paint systems hold up to our rough marine conditions.
Another water-based test is tide water testing. This is where the plastic part is immersed in water for a set length of time and then is checked at scheduled intervals for paint swelling, blistering or other damage. It’s a good comparative testing for paint systems to see how the part reacts. Originally used more for metals, it’s been applied to plastic parts more and more over the years after realizing that there are some chemistries that just don’t work well in water. For example, traditional urethanes can swell or blister – in which case, that’s not the paint you want.
What new trends have you seen develop with painting/coatings in the last few years?
In the last few years, there has been a big shift away from acrylic paints to urethanes for paint on plastics. Urethanes are more chemically resistant, and they have better UV resistance, both of which play a big role from the performance side of things. Urethanes also cure at a much lower temperature than traditional acrylics. For some composites, like sheet molding compound (SMC), switching to low-bake paint allows for improved line efficiency because operators don’t have to worry as much about the defects associated with higher curing temperatures.
There also has been a definite shift toward more “green” and/or environmentally friendly paint chemistry. It might not be something that always directly impacts the plastic part, but sustainability is becoming a huge part of the market. When it comes to paint systems for plastics, more and more the kind of solvents being used and the amounts used in the systems are being scrutinized for sustainability.
Are there any new technologies in painting/coating equipment?
About 20 years ago, going into a paint shop would have meant seeing a couple of really good operators spraying the part, doing things more by hand. Now, most shops will have robots doing the spraying. This has been a huge shift away from human operators, and it has led to less contamination of the sprayed part. With fewer people opening and closing doors, handling the part, etc. there is a lot less room for human error.
There also has been a huge shift away from air atomizing spray guns in favor of high-volume/low-pressure systems (HVLP). As with the shift to urethanes, this has led to improved transfer efficiency and improved orange peel. With air atomizing systems, there was about 30 to 40% transfer efficiency. With HVLP, that increased to about 50 to 60% efficiency. And now, with more shops using rotary bell spray guns, some claim transfer efficiency above 90%. That has been the most dramatic switch over the years with paint applications on plastics.
Akriti Agarwal serves as the global manager – paint and coatings for Mercury Marine. As a member of the Brunswick Corporation, Mercury Marine is one of the world’s leading providers of marine propulsion. At present, Mercury product brands include Mercury, Mercury Racing, MerCruiser and Mariner outboards (sold outside the US). For more information, visit www.mercurymarine.com.